Releasing the Potential of Steel Stamping: Professional Tips and Finest Practices Revealed
In the world of metal marking, where accuracy and efficiency preponderate, the pursuit to enhance processes and unlock surprise capacities is a perpetual search. Expertise sharpened over years of market experience, incorporated with cutting-edge methods and advanced technologies, holds the crucial to achieving unmatched results. As we browse with the detailed world of steel stamping, a closer consider the ins and outs of tooling design, product selection, production performance, quality control, and arising trends guarantees a bonanza of insights waiting to be uncovered. Stay tuned to find just how these professional pointers and best methods can revolutionize the metal marking landscape.
Tooling Layout Optimization
Maximizing tooling layout is important for improving performance and accuracy in steel marking procedures. A well-balanced tooling design can considerably affect the high quality and cost-effectiveness of metal marking procedures. By meticulously considering elements such as material selection, die configuration, and part geometry, manufacturers can streamline production processes and improve overall item top quality.
One key facet of tooling layout optimization is picking one of the most appropriate materials for the punches and dies used in the marking procedure. Products with high wear resistance and durability are chosen to guarantee longevity and minimize tooling upkeep demands. Furthermore, die configuration plays an essential role in attaining harmony and uniformity in stamped parts. Proper die design can aid protect against concerns such as wrinkling, tearing, and too much springback, causing higher production returns and lowered scrap rates.
Moreover, optimizing component geometry through tooling layout can help decrease material waste and production time. By meticulously shaping passes away and punches to match the preferred component specs, manufacturers can attain tighter tolerances and boosted part top quality. In general, spending time and resources in maximizing tooling design can cause significant lasting benefits for steel stamping operations.

Product Option Methods
Purposefully picking products for steel marking tooling is paramount for making sure longevity and efficiency in manufacturing procedures. When selecting materials for metal marking applications, numerous key factors should be taken into consideration. The very first consideration is the sort of product being marked. Different products, such as light weight aluminum, stainless steel, or copper, require certain tooling materials to make sure ideal efficiency and durability.
One more critical variable in product choice is the expected manufacturing volume - Metal Stamping. For high-volume production runs, tooling products with remarkable wear resistance and strength, such as device steels or carbide, are usually liked to stand up to the rigors of continual stamping operations
Moreover, the complexity of the marking layout and the needed precision additionally play a considerable role in product selection. For detailed stamping patterns or limited tolerances, products with high thermal conductivity and excellent machinability, like beryllium copper or device steel alloys, may be extra appropriate to attain the desired outcomes.
Production Performance Methods
To enhance making result and reduce manufacturing prices, executing reliable strategies in metal stamping procedures is crucial. One vital approach for improving production efficiency is investing in automation. Automated metal marking makers can execute tasks with precision, consistency, and at a much faster rate than manual work, causing boosted performance and lowered cycle times. Additionally, implementing predictive maintenance practices can help avoid unforeseen discover here downtime by determining prospective devices failings prior to they happen. By routinely checking equipment efficiency and attending to check here concerns proactively, makers can maximize manufacturing routines and lessen interruptions.
Another strategy to improve manufacturing performance is with continuous procedure enhancement. Performing routine audits and efficiency examinations can help recognize traffic jams, inefficiencies, and areas for improvement within the metal marking procedure. By examining data and responses from these examinations, makers can execute targeted services to streamline procedures, boost throughput, and make best use of general performance.
Moreover, adopting lean production concepts, such as 5S methodology and Kanban systems, can assist eliminate waste, enhance operations, and improve total efficiency in steel stamping procedures. By cultivating a culture of continual improvement and equipping staff members to contribute concepts for efficiency gains, producers can open the full capacity of their steel marking processes.
Top Quality Control Steps
Structure on the foundation of effective manufacturing methods in steel stamping procedures, guaranteeing rigorous quality assurance actions is necessary for maintaining item standards and client complete satisfaction. Quality control in steel stamping includes methodical inspection, testing, and surveillance of the production processes to determine and fix any type of inconsistencies or problems that can jeopardize the end product's honesty (Metal Stamping). Executing actions such as regular tools maintenance, in-process evaluations, and detailed screening of finished parts can aid detect problems beforehand and protect against costly rework or product recalls
Regular audits and testimonials of high quality processes can aid determine locations for website link enhancement and guarantee uniformity in item quality. By cultivating a society of quality consciousness among staff members and offering adequate training on top quality control treatments, manufacturers can boost overall item dependability and brand name track record.

Innovative Metal Stamping Technologies
Developments in metal stamping modern technologies have actually reinvented the production market, boosting effectiveness and precision in the production procedure. Servo presses supply unparalleled control over the marking procedure, enabling for modifications in dwell, pressure, and speed time with exceptional precision.
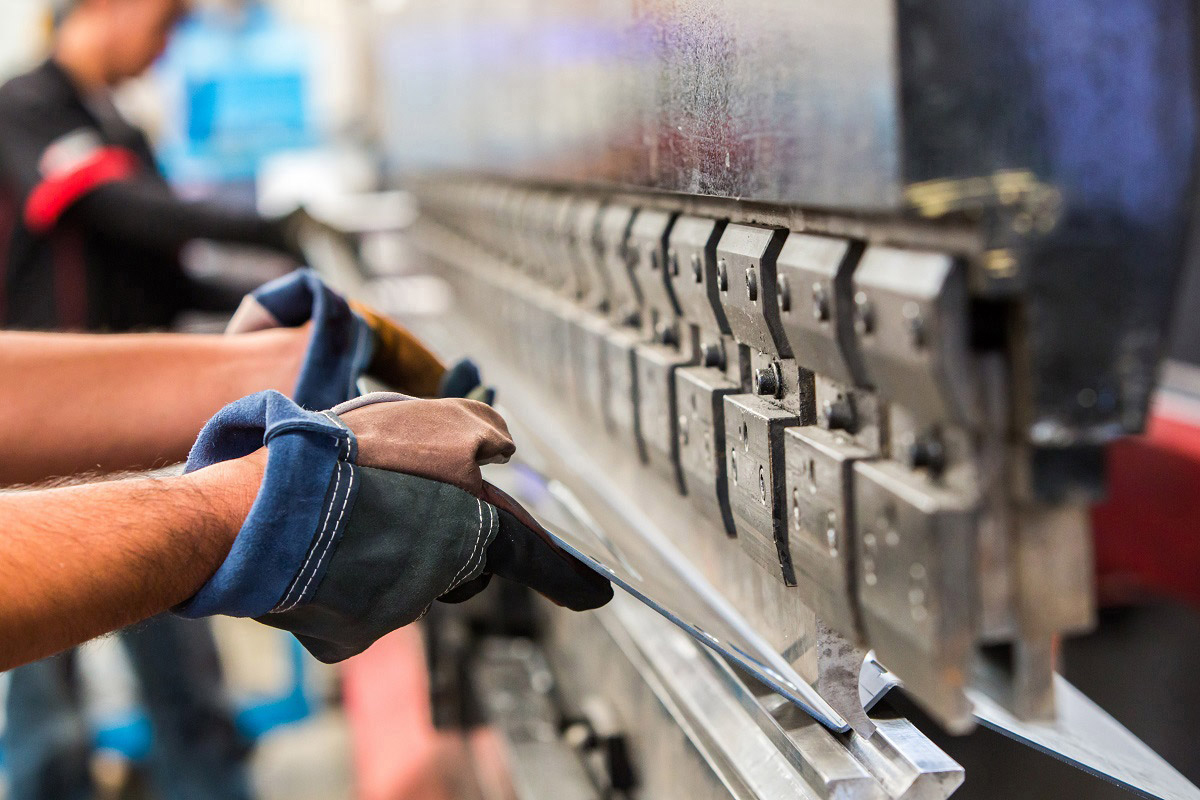
Furthermore, the fostering of additive production techniques in metal stamping, such as 3D printing of die components, has streamlined the tooling style and manufacturing procedure. This strategy enables greater design flexibility, fast prototyping, and expense financial savings in tooling manufacturing. By leveraging these cutting-edge technologies, manufacturers can unlock new levels of efficiency, quality, and competitiveness in the metal stamping sector.
Conclusion
In conclusion, the optimization of tooling design, strategic material selection, efficient manufacturing strategies, quality assurance actions, and cutting-edge technologies are important for unleashing the full possibility of steel marking. By applying these ideal techniques and experienced pointers, suppliers can boost performance, raise top quality, and stay affordable in the steel marking market. It is essential for companies to continually review and enhance their processes to achieve success in this area.
As we navigate with the intricate globe of metal marking, a more detailed look at the ins and outs of tooling design, product choice, production performance, high quality control, and arising patterns guarantees a treasure chest of insights waiting to be uncovered. A well-balanced tooling design can dramatically affect the quality and cost-effectiveness of steel stamping procedures.Building on the structure of effective production strategies in metal marking processes, ensuring rigorous top quality control measures is vital for maintaining item standards and consumer fulfillment. Quality control in metal marking involves methodical inspection, testing, and surveillance of the manufacturing refines to identify and correct any kind of discrepancies or defects that might endanger the final item's integrity.In final thought, the optimization of tooling layout, strategic product option, efficient production strategies, quality control actions, and cutting-edge technologies are necessary for unleashing the full capacity of steel marking.